Poly Crystal Diamond Wafers: Innovation at the Atomic Level for Diamond Industries
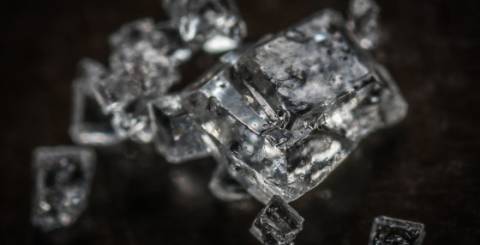
In the rapidly advancing landscape of high-tech manufacturing, electronics, and materials science, diamonds are no longer just gemstones they’re high-performance materials redefining what’s possible in technology. Among the most transformative innovations in this space are Poly Crystal Diamond Wafers (PCD wafers), a material that blends the legendary hardness of diamond with scalability and engineered functionality.
For Diamond Industries, which operates at the intersection of precision materials and industrial applications, poly crystal diamond wafers represent an exceptional opportunity to lead in next-generation technology, from power electronics to quantum computing. This article delves into what PCD wafers are, their advantages, manufacturing methods, and the wide array of industries where they’re making a revolutionary impact.
What Are Poly Crystal Diamond Wafers?
Poly Crystal Diamond Wafers, also known as polycrystalline diamond wafers, are thin slices of material composed of numerous microscopic diamond crystals, or "grains," fused together. Unlike single-crystal diamonds, which are uniform in structure, polycrystalline diamonds consist of many randomly oriented crystal grains that are tightly bonded to form a dense, coherent wafer.
These wafers are typically synthesized using chemical vapor deposition (CVD) techniques and then sliced and polished to precise thicknesses. The resulting material retains many of the superlative properties of diamond such as exceptional hardness, thermal conductivity, and chemical resistance but at a cost and scale suitable for industrial deployment.
Manufacturing Poly Crystal Diamond Wafers
The most common method for producing PCD wafers is CVD (Chemical Vapor Deposition). In this process:
- A substrate (often silicon or molybdenum) is placed in a vacuum chamber.
- Carbon-containing gases such as methane are introduced.
- The gases are activated using microwave plasma, causing carbon atoms to deposit and crystallize on the substrate surface.
- Over time, a layer of polycrystalline diamond forms and can be cut into wafers of varying thickness.
This process allows for fine control over grain size, purity, and layer thickness, making it possible to tailor the diamond film for specific mechanical, optical, or electronic applications.
Properties of Poly Crystal Diamond Wafers
Polycrystalline diamond wafers offer a compelling set of properties, making them ideal for demanding industrial and technological environments:
1. Extreme Hardness and Wear Resistance
PCD wafers exhibit hardness second only to natural diamond, making them excellent candidates for cutting, drilling, and wear-resistant surfaces in high-stress environments.
2. High Thermal Conductivity
Diamond is the best known thermal conductor. PCD wafers are ideal for heat sinks, thermal management substrates, and high-power electronics where heat dissipation is critical.
3. Chemical and Corrosion Resistance
Due to their inertness, PCD wafers perform exceptionally well in corrosive environments, from semiconductor fabs to oil drilling operations.
4. Optical Transparency
Depending on grain size and purity, PCD wafers can be transparent in the infrared and visible spectrum, making them useful in optics and laser windows.
5. Electrical Insulation
While diamond is an excellent insulator, PCD wafers can be doped to provide semiconducting properties, opening new paths in high-frequency and high-voltage electronics.
Applications of PCD Wafers Across Industries
1. Electronics and Semiconductors
PCD wafers are emerging as a solution in high-power, high-frequency electronic devices due to their ability to dissipate heat far more efficiently than traditional substrates like silicon or gallium nitride. Applications include:
- Power amplifiers
- RF devices
- Insulated gate bipolar transistors (IGBTs)
2. Quantum Computing
Diamond is a frontrunner in quantum computing research due to nitrogen-vacancy (NV) centers, which act as stable qubits. PCD wafers with controlled impurity levels are now being developed to host quantum bits for advanced computing architectures.
3. Thermal Management Systems
In advanced aerospace and defense systems, managing heat is critical. PCD wafers are used as:
- Heat spreaders in avionics
- Thermal interfaces for satellites
- Laser diode cooling substrates
4. Optics and Photonics
Because of their optical clarity and robustness, PCD wafers are ideal for:
- Infrared windows
- Beam splitters
- Laser protection optics in high-energy environments
5. Cutting and Drilling Tools
PCD is already widely used in cutting tool inserts, drill bits, and machining equipment. PCD wafers provide a standardized, scalable material that can be cut and shaped into precise tool geometries.
6. Biomedical Devices
Diamond's biocompatibility makes PCD wafers suitable for implantable sensors, drug delivery systems, and wearable medical electronics that require stable, long-lasting materials.
Advantages for Diamond Industries
For a company like Diamond Industries, investing in PCD wafer technology provides a strategic edge on multiple fronts:
- Scalable Innovation: CVD-grown PCD wafers allow mass production of diamond-quality materials without reliance on rare, costly natural stones.
- Customization: PCD wafers can be engineered for specific needs—grain size, surface finish, electrical conductivity—making them a versatile product for custom clients.
- Cross-Industry Versatility: With demand spanning semiconductors, defense, energy, and healthcare, the market potential for PCD wafers is immense.
- Sustainability: Synthetic diamond wafers minimize mining-related environmental impact while offering superior performance characteristics.
Future Outlook and Innovation Trends
The market for PCD wafers is projected to grow rapidly, driven by the need for efficient thermal management, high-performance electronics, and durable materials in increasingly demanding environments.
Emerging research is exploring:
- Doping strategies for tunable electrical properties
- Nano-grained PCD for improved optical transparency
- Integration with MEMS and NEMS devices
- Flexible diamond films for wearable tech and next-gen displays
Diamond Industries, with the right R&D and manufacturing investments, is well-positioned to be a market leader in this transformative technology.
Conclusion
Poly Crystal Diamond Wafers are not just another industrial material they're a platform for innovation across some of the most exciting fields in science and engineering. Their unique properties bridge the gap between durability and functionality, offering solutions where traditional materials fall short.
For Diamond Industries, embracing and leading the development of PCD wafers means entering a future defined by precision, performance, and possibility. From powering tomorrow’s electronics to enabling breakthroughs in quantum computing and photonics, Poly Crystal Diamond wafers are at the heart of the diamond-driven revolution.
Similar Articles
Explore CNC turning—its components, process, benefits, applications, and future trends shaping modern precision manufacturing in various industries.
In the competitive industry of car manufacturing, attaining exceptional performance along with an innovative design needs the incorporation of modern manufacturing technologies
Facing delays, quality issues, or supply chain problems in hardware manufacturing? Learn the top 7 challenges—and practical fixes—to streamline production.
A business in the manufacturing industry today has to ensure that it chooses the precision-engineered components suppliers keenly since the competition is very stiff
Selective Laser Sintering, or SLS, has established itself as one of the most reliable and widely used 3D printing technologies. This method is valued for its ability to produce complex, durable, and high-quality parts without the constraints of traditional manufacturing.
In the retail and display industry, the visual appeal of products is paramount. Customers are constantly drawn to displays that are not only eye-catching but also provide an immersive experience.
As previously established, CO2 laser technology operates by shining a high-power infrared beam on a mixture of gas that contains carbon dioxide, nitrogen, and helium. This technology is well known for the fact that it is able to engrave onto a variety of materials such as wood, glass, plastic, leather, and even some metals with high precision and without contact.
CNC Machining has emerged as a vital technique in the current production process, as it provides an efficient and accurate means of manufacturing items with complex geometries. This technology is applied across aerospace, automobile, and medical devices manufacturing fields, and various other industries.
Find out what to look for in a reliable CNC machining manufacturer, from quality assurance and advanced technology to customer service, for efficient project success.