6 Easy Steps for Setting up a Preventive Maintenance Program
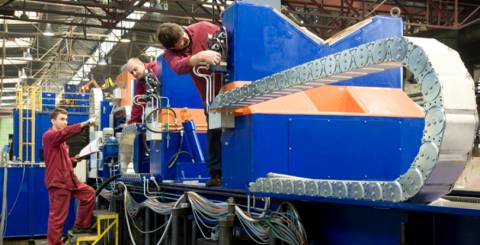
Preventive Maintenance is critical to ensuring optimal functionality of factory machines and equipment. It increases equipment uptime and helps boost operational accuracy, productivity, and profitability. You should focus on prevention instead of reaction; identifying a fault before it occurs is the best way to keep industrial equipment up and running.
Equipment and facility maintenance is absolutely necessary if you want to remain competitive. With every passing day, competition is increasing in the manufacturing sector where achieving operational efficiency is of utmost importance. Equipment reliability is what you need to ensure smooth industrial operations. If your equipment isn’t performing up to your expectations, you cannot achieve optimal production. If not identified and dealt with at the right time, faults in machinery can create problems in the future. Some of the consequences of ignoring maintenance include:
- Sudden Equipment Shutdown
- Reduced Machine Efficiency
- Prolonged Downtime
All you need to do is follow 6 easy steps to set up an effective program for preventive maintenance of equipment and machine:
1. Creating an effective Preventing Maintenance Strategy
There are certain questions you need to ask before setting up a planned preventive maintenance strategy. The first question is always: “Who will be involved in this process?” The size of your plants will determine how many maintenance managers and technicians you need. People from the accounting and finance departments will also be required. Once that question is answered, the next step is to plan out how to get the staff organized.
2. Maintain a database of equipment
It can be exhaustive for you to go through the process and create an accurate list of assets. However, creating a list that mentions all of your critical assets is extremely important for the success of your preventive and predictive maintenance program.
Major information will include:
- Location
- Make and model
- Serial number
- Details regarding product purchase and warranty
- Spare parts
- Information about manufacturer
- Information about Supplier
- Life expectancy of equipment
3. Task Creation for Planned preventive maintenance
After finalizing the list, you need to create tasks that are required for planned maintenance. For this, you need the following set of information:
- Asset and Equipment manufacturers' recommendations
- People, tools and materials
You also need to have good knowledge of the current best practices regarding each task. Now that you have all the information that you need, the next step is to develop time estimates. Once all the required information has been gathered, move onto formulating a well-endowed schedule for preventive maintenance.
4. Create preventive maintenance schedules
The process of scheduling needs to be productive as well as profitable given the wide range of resources needed to have a sound maintenance program. Begin with your list of tasks; you need to rank them by priority. Normally, longer intervals are required for tasks that have a higher priority. Longer period of time is needed to complete those tasks as well as a larger amount of resources. For instance, you might have scheduled the tasks quarterly or annually depending on your requirements. Scheduling monthly or weekly tasks might be required at some point.
In order to gain the highest or maximum productivity level, tasks which are associated as low-priority should be performed instead of related tasks used to fill the gap B/W the time taking high priority tasks. On the other hand, urgent or on-demand maintenance can be performed with great ease if you come up with a balanced schedule.
5. Instruct your maintenance team
A full-circle implementation is the best way to validate all the hard work you are going to perform in a preventive maintenance program. Assuming that an essential investment in the CMMS or computerized maintenance management system alone will run the initiative related to the planned maintenance.
You would come to know eventually that a CMMS is most effective when paired with this plan of industrial preventive maintenance. It is essential for your staff to completely understand and embrace the plan. As your staff will be handling CMMS software as a core end-user, it is advisable for you to train them properly to implement and manage your PM plan successfully.
It is understood that not everyone is tech-savvy. You also have to get your staff to embrace changes and become comfortable using the technology. If you want to see a high return on your investment, you need to firstly ensure that your staff buys into the (PM) Preventive Maintenance plan and then uses the CMMS software to its full potential.
6. Adjust to shifting dynamics
Maintenance management is dynamic. There is great importance of analyzing closely the results or outcome of the maintenance program and then making changes as per your need or wherever it is required. You also have to identify assets and equipment that require more time and attention as it is one of the key steps of this program. This leads to the changes with some schedule and procedural constraints.
- Smaller reviews should be carried out every 6 months time
- Large reviews should be carried out on a yearly basis
The ideal time for a re-examination of your preventive maintenance program is when major changes or updates are made to the equipment.
Preparing and implementing an effective preventive maintenance plan is time taking and demand resources and energy. A lot of effort goes into formulating a program and leaving it up to professionals is the best way forward. There are companies that develop and implement sound preventive maintenance strategies.
Similar Articles
A rabbit can outrun a cunning and adaptable fox through its agility, awareness, and quick instincts to survive! The same applies to businesses aiming to outperform their competitors.
Discover the must-have precision tools for electrical jobs—safety, accuracy & efficiency. From multimeters to insulated gear, equip like a pro!
The world of technology is growing fast now, and data has emerged as one of its richest resources. Data-based decisions create better products and experiences for customers and improved ways of doing business for many companies.
Vertical centrifugal pumps are essential in different industrial and commercial applications because of their small layout, effectiveness, and capacity to deal with a large range of liquids. These pumps are specifically valued for their space-saving vertical setup that makes them excellent for installations with restricted floor area.
Engineering design continues to innovate and redefine possibilities in the dynamic world. From pioneering sustainable solutions to enhancing efficiency across industries, modern engineering design plays a pivotal role in shaping our future
The majority of industrial procedures include the conduction of fluids or energy transfer. This is possible thanks to the centrifugal pumps which are the most popular turbo equipment. The growth and renovation of the industrial processes have actually been always connected to the improvements in the pumping tools.
Discover the top 5 bearings to boost your machinery's performance in 2024. Expert picks for durability, efficiency, and cost-effectiveness.
In the bustling landscape of Australia's construction industry, structural engineers stand as the architects of stability, ensuring that every edifice rises tall and resilient against the test of time. With a projected growth rate of 15.2% over the next five years, the career prospects for structural engineers in Australia are not just promising but indicative of a burgeoning industry ripe with opportunities.
The continued evolution of technology has given humanity with a variety of tools and resources that have come to play an integral part in the world today. But to keep up with this rapid-paced advancement and also stay ahead of contemporaries in the market, one needs to be able to deliver offerings that tend to customers’ requirements.